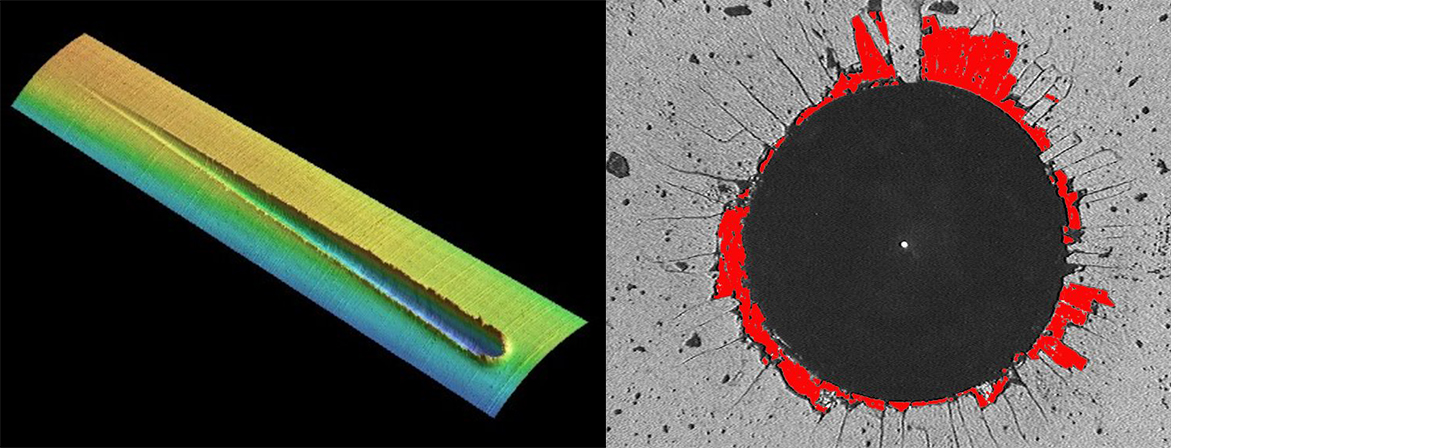
Beim Scratchtest wird ein Diamantstift mit steigender Last über die Oberfläche gezogen. Dabei werden mechanische Spannungen zwischen Schicht und Substrat erzeugt, die beim Überschreiten einer kritischen Grenze zu Schichtabplatzungen führen. Diese kritische Last dient als Maß für die Haftung und wird durch Inspektion im Mikroskop bestimmt. Neben Last und Eindringtiefe wird beim Scratchtest auch der Reibungskoeffizient und die beim Scratch erzeugte akustische Emission detektiert, die bei der Auswertung unterstützen können. Mit dem Gerät kann auch die Kratzbeständigkeit von Oberflächen geprüft werden.
Beim Rockwelltest wird ein konischer Diamantindentor mit definierter Kraft in die Schichtoberfläche eingedrückt. Auch hier entstehen um den Eindruck herum Abplatzungen, die nach verschiedenen Normen und Richtlinien ausgewertet werden können. Der Rockwelltest ist wie der Scratchtest schnell und einfach anzuwenden, aber nur für harte und spröde Schichten geeignet. Für weiche Metalle oder Lacke sind eher der Gitterschnitt-Test oder der Stirnabzugstest zu empfehlen, die ebenfalls verfügbar sind.
Weiterhin stehen zur Verfügung:
Die Gitterschnittprüfung ist eine einfache Methode zur Bestimmung der Haftfestigkeit von Beschichtungen. In die zu testende Beschichtung wird mit einer Mehrfachklinge ein kreuzweises Gitter geritzt. Nach erfolgreicher Gitterschnittprüfung wird die Oberfläche gesäubert und zusätzlich ein in der Norm definiertes Klebeband auf das Schnittraster geklebt und abgezogen. Die Auswertung der Prüfung erfolgt visuell (DIN EN ISO 2409) nach der Anzahl der abgeplatzten Quadrate und dem Erscheinungsbild. Je nach Zustand des Schadensbildes unterscheidet man Gitterschnitt-Kennwerte von 0 (sehr gute Haftfestigkeit) bis 5 (sehr schlechte Haftfestigkeit).
Der Stirnabzugstest ermöglicht eine quantitative Charakterisierung der Schichthaftung. Metallische Stempel (Ø20 mm) werden mittels eines 2 Komponentenklebers auf die Beschichtung aufgeklebt. Nach Aushärten wird die zum Abreißen des Stempels erforderliche Kraft gemessen. Die abgerissene Fläche wird vermessen und deren Wert weiterverwendet, um die Haftfestigkeit (N/mm2) der Beschichtung zu berechnen. Voraussetzung für diese Prüfmethode ist eine stabile Klebung zwischen dem Stempel und der Schichtoberfläche.
Auf einer beschichteten Oberfläche wird ein Klebeband mit definierter Haftfestigkeit fest aufgeklebt und im Anschluss ruckartig abgezogen. Bei einer guten Haftung auf dem Untergrund finden sich kaum Rückstände des Beschichtungsmaterial am Klebeband, während bei einer schlechten Haftung das Beschichtungsmaterial am Klebeband haften bleibt. Ist das Beschichtungsmaterial sowohl an der Oberfläche des Untergrundes, als auch auf dem Klebeband sichtbar, resultiert dies vermutlich aus einem Mangel an Kohäsion innerhalb der Schicht. Der Tapetest dient der qualitativen Orientierung.