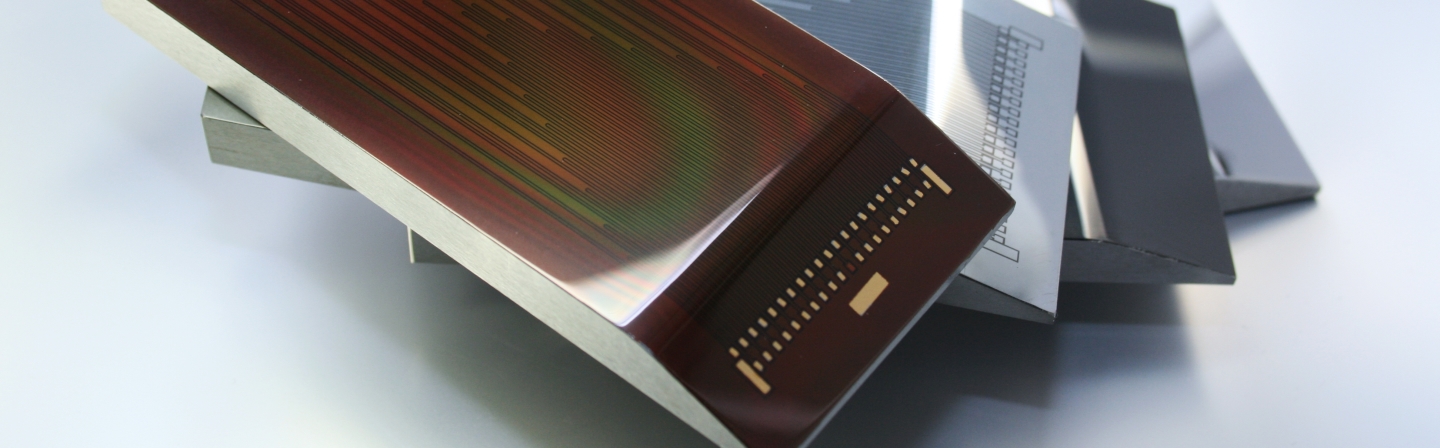
Die Messung von Kraft, Druck, Temperatur, Verschleiß und weiteren Größen direkt in Hauptbelastungszonen oder auf Werkzeugaktivflächen mittels Dünnschichtsensorik liefert wertvolle Daten, um bestehende Produktionsprozesse oder Simulationsmodelle zu optimieren. Der Einsatz verschleißfester und tribologisch angepasster Dünnschichtsensoren ermöglicht die Messung in bisher schwer zugänglichen Bereichen.
Unsere dünnschichtbasierte Sensortechnologie bietet ideale Voraussetzungen für anwendungsorientierte Lösungen rund um industrielle Produktionsprozesse. In den letzten Jahren steigt die Nachfrage aus der Industrie nach Sensorik, die direkt auf Bauteiloberflächen in Kontakt mit dem Werkstück eingesetzt wird, um lokal Messdaten auch während des Prozesses erfassen zu können. Im Fokus unserer aktuellen Entwicklungen steht daher eine individuell angepasste Sensortechnik zur umfassenden Digitalisierung für autonome und selbststeuernde Produktionssysteme.
Am Fraunhofer IST entwickeln wir multifunktionale Dünnschichtsensorsysteme für die lokale Messung der Druck- und Temperaturverteilung auf der Oberfläche z.B. von Werkzeugen. Dabei handelt es sich um ein verschleißfestes Mehrschichtsystem, das besonders in hochbelasteten Bereichen sowie auf komplex geformten Oberflächen die Messdaten erfassen kann. Gemeinsam mit unseren Kunden entwerfen wir ein individuelles Sensordesign, sodass die Module einfach in bestehende Maschinen integriert werden können und das Schichtsystem direkt auf Oberflächen von 2D- und komplex geformten 3D-Bauteilen appliziert werden kann. Auf Basis unterschiedlicher physikalischer Wirkprinzipien bringen wir dünnschichtbasierte Sensoren und Sensorsysteme in Ihre Anwendung, wobei hochbelastete Bereiche und raue Umgebungsbedingungen im Fokus stehen. Für die Herstellung unserer Sensortechnik decken wir die gesamte Prozesskette von Substratvorbehandlung, Reinigung, Beschichtung sowie die abschließende Kalibrierung ab. Insbesondere verfügen wir über umfangreiche Kompetenzen für die Erzeugung von Mikrostrukturen und nutzen dafür vielfältige Strukturierungsverfahren und -techniken im eigenen Reinraum.
Die am Fraunhofer IST entwickelten Dünnschichtsysteme ermöglichen Ihnen die In-situ-Echtzeiterfassung von Prozessdaten in Hauptbelastungszonen zur Optimierung von Simulation und Produktionsprozessen sowie zum Zustandsmonitoring. Bei Interesse sprechen Sie uns gerne an.
Anna Schott M.Sc. / Gruppenleiterin
Zukünftig wird unsere Sensortechnik für neue Anwendungsfelder im Bereich der Energietechnik und Elektromobilität weiterentwickelt. Parallel werden die notwendigen Schritte zur Skalierung aktueller Lösungsansätze für den erfolgreichen Technologietransfer in die Industrie im Sinne des Selbstverständnisses von Fraunhofer als industrienahen Forschungspartner erfolgen. Dazu werden stückzahlfähige Prozesse und die dazugehörigen Produktionstechniken entwickelt und als flexible Fertigung aufgebaut. Dabei steht die Digitalisierung der gesamten Prozesskette bis hin zur Entwicklung cyber-physischer Systeme im Fokus. Durch tribologische Optimierungen der gesamten Prozesskette können erzielte Effizienzgewinne einen direkten Beitrag zur Erreichung von Nachhaltigkeitszielen leisten.