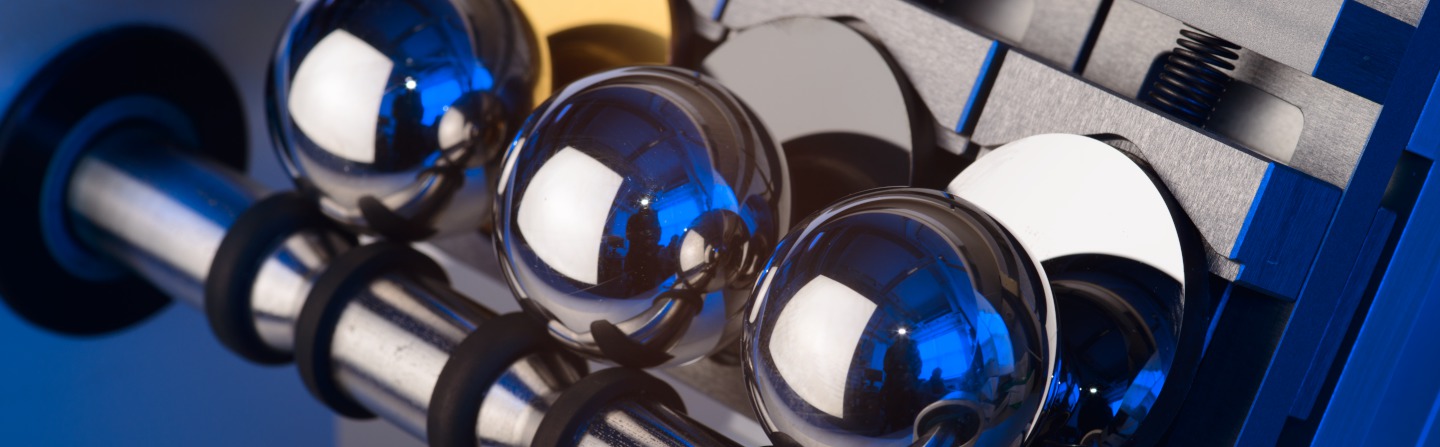
Mit dem Kalottenschliffverfahren lässt sich die Verschleißbeständigkeit von Schichten und Oberflächen präzise bestimmen. Eine mit Abrasivflüssigkeit benetzte Stahlkugel, die sich gegen die Probe dreht, schleift eine Kalotte (Kugelkappe) in die zu prüfende Schicht. Aus dem Volumen der Kalotte lässt sich der Verschleißkoeffizient berechnen.
Das Verfahren eignet sich zur Prüfung von Schichten mit Schichtdicken ≥ 1 μm. Der Abrasivverschleiß reagiert sehr empfindlich auf Änderungen der Schichtzusammensetzung und Struktur. Er kann daher als Kenngröße für die Bewertung der Schichtqualität in der Fertigung und zur Optimierung während der Entwicklung von Schichtsystemen herangezogen werden.
Wird die Kalotte durch die Schichten hindurch bis in das Substrat eingeschliffen, so kann aus den Durchmessern der Ringe die Dicke der Schichten bestimmt werden. Die Genauigkeit der Schichtdickenmessung beträgt je nach Oberfläche ca. 0,1 µm.
Wird die Kalotte durch die Schichten hindurch bis in das Substrat eingeschliffen, so kann aus den Durchmessern der Ringe die Dicke der Schichten bestimmt werden. Die Schichtdicke t ergibt sich dann aus der Formel: t = (D2-d2)/8R, wobei D, d = äußerer und innerer Ringdurchmesser und R der Kugelradius ist. Die Genauigkeit der Schichtdickenmessung beträgt je nach Oberfläche ca. 0,1 µm.