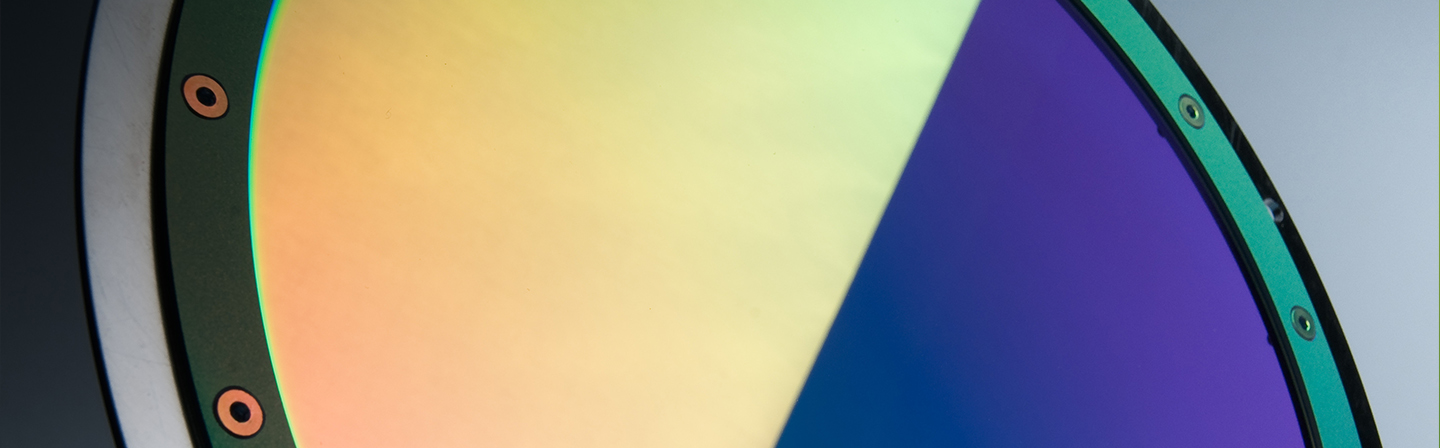
For the widest variety of applications of optical components, thin-film technologies provide an important contribution towards the development of innovative solutions. Across all sectors, optical components are just as necessary for automated production processes as for the application itself. This requires layers – ranging from one single layer to several hundred – which are stable against environmental influences and which must be deposited with an accuracy of only a few atomic layers. At the Fraunhofer IST, we develop such precision optical systems and the associated production processes.
With the coating platform EOSS® (Enhanced Optical Sputtering System), a production-ready system for high-precision interference filters is available and, in combination with the process monitoring and control software MOCCA+®, complex filters with many hundreds of layers can also be achieved, which we design based on the requirements of our customers. For the optimization of processes and facilities we create customized simulations and virtual coating runs. We link these with optical measurement technology for process control and quality assurance.
Dr. Michael Vergöhl, Head of Department