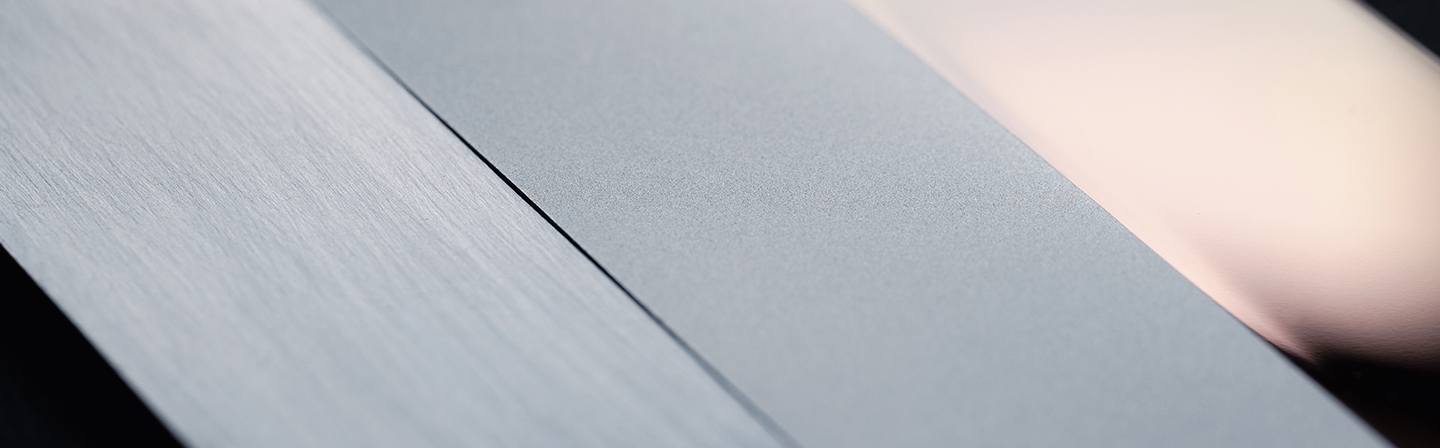
The demands on technical surfaces are growing continuously and thus increasingly require the combination of a wide variety of surface technologies. As functional tribological surfaces always interact with counter bodies or fluids, an application-adapted adjustment of the topography is necessary. Surface-machining processes such as milling, turning and grinding are frequently incapable of creating the required functional topographies, that is why smoothing procedures such as blasting, polishing or electrochemical processes are employed in the case of tools or components for highly stressed tribological applications. The Fraunhofer IST is therefore developing solutions for application-adapted topography adjustment by means of technology combinations and the consideration of the material, diffusion and coating technology, lubricant selection and stress profile.
The surface topography has a significant influence on various properties such as the coefficient of friction, the wear behavior such as abrasion or adhesion, the coating adhesion, the corrosion behavior, the gloss, and the appearance of the surface. Only the interaction of the selected application-specific technology combinations in dependence on the material behavior can result in in the creation of optimal solutions for differing applications.
Technical surfaces are often polished in a time-consuming and cost-intensive process in order to fulfill specified surface characteristics. Blasting, in contrast, enables the rapid and cost-effective structuring of surfaces or the targeted introduction of lubrication pockets that support a hydrodynamic lubricant-film formation in order to minimize friction and wear. Furthermore, shot-blasted surfaces improve the layer bonding of physical vapor deposition (PVD) or plasma-assisted chemical vapor deposition (PACVD) coatings. Applied structures can be preserved through wear-resistant hard-material coatings and can therefore be utilized more durably on tools and components.
Various analysis methods serve the determination of the roughness and topography of the surface. At the Fraunhofer IST, a comprehensive range of measuring technologies is available for surface measurement. This includes tactile and optical measuring methods, confocal laser and light microscopy or scanning electron microscopy (SEM) with integrated elemental analysis (EDX).
Shot-blasting is an environmentally friendly, cost-effective and economical process. Furthermore, it can be easily automated and integrated into the workflows of series production. Shot blasting is used to clean surfaces or to specifically create a desired surface topography. By means of differing blasting techniques, such as pressure and injector blasting, surfaces can be leveled and structured. Widely varying mineral, metallic and biological blasting materials in graded grain sizes are thereby utilized. The blasting media each have their own specific advantages and can be selected in accordance with the application at hand. A distinction can hereby be made between abrasive blasting media, such as silicon carbide, and gentle blasting media, such as glass beads.
With dry electropolishing, the Fraunhofer IST has a new technology at its disposal for the surface finishing of metallic surfaces. With DryLyte technology, uniformly polished surfaces can be created. In contrast to classic wet-chemical electropolishing, DryLyte uses a dry electrolyte granulate which contains only small traces of acids and which is therefore more environmentally friendly. The process is suitable for various materials, which can be either conventionally or additively manufactured. Examples include tool or stainless steels, aluminum and copper, which can be additionally coated or plasma-nitrided. With this process, high surface qualities (e. g. Ra ≤ 0.03 μm, Rz ≤ 0.3 μm, Rpk, Rvk ≤ 0.05 μm) or specific topographies can be achieved.