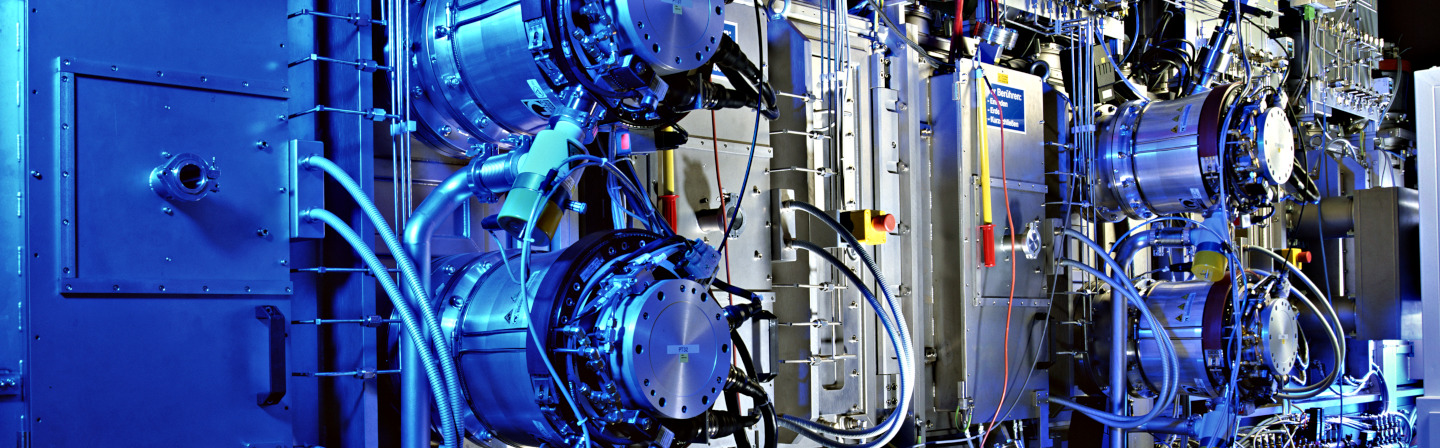
The Fraunhofer IST brings together unique expertise in the industrial use of magnetron sputtering. From applications for friction reduction or protection against corrosion and wear, through electrical and optical functions, and on to medical technology, the different variants of magnetron sputtering are utilized. Diverse coating sources, as well as process monitoring and active control, are applied and further developed at the Fraunhofer IST.
For development purposes, industrial coating facilities in batch and inline type with different source geometries (planar and cylindrical cathodes) for metallic and reactive deposition are available.
With the sputtering system EOSS® (Enhanced Optical Sputtering System), Fraunhofer IST made a step forward in high precision optical coating production. The coatings are deposited in a turntable system in up to three chambers by means of magnetron sputtering. Using rotatable targets as source material, the compound-assisted reactive magnetron sputtering (CARS) process results in a stable thickness uniformity of better than ± 0.2 % over 200 mm substrates. Rotatable sputtering in combination with a sputter-up configuration guarantees minimized particle contamination. The EOSS® system is equipped with a plasma source for oxidation and substrate pretreatment as well as with a high-performance heating system. A broadband optical monitor and the MOCCA+® control software are implemented for fully automated deposition.
The experts at the Fraunhofer IST utilize the A700V inline-sputter coating facility for the research and development of coatings and complex coating systems on an industrial scale. This ranges from material and process development of single layers through to systems of up to 10 different materials, e.g. for transparent conductive oxides (TCO), low-e layer systems, electrochromics, solar protection, fuel cells, interference optics on a large area or astronomy mirrors.
The Megatron® coating module developed at the Fraunhofer IST allows the rapid and variable realization of previously unattainable combinations of materials. Behind each of the two cylindrical tube targets, a further planar target is arranged. In the secondary sputtering process, atoms are detached from the planar target and “implanted” into the tube target. Titanium oxide, for example, can be doped with niobium and deposited. For certain material combinations, this results in an increased sputtering rate of up to 100 percent compared to the conventional process. The new module is ready for series production and can be retrofitted.