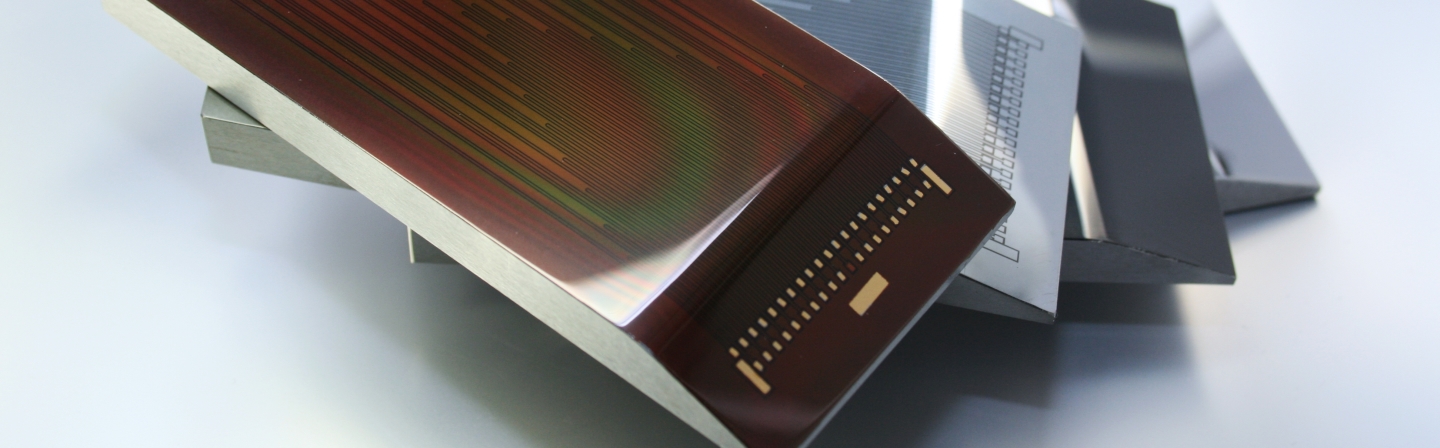
The measurement of force, pressure, temperature, wear and other variables directly in main load zones or on tool active surfaces provides valuable data by means of thin-film sensor technology in order to optimize existing production processes or simulation models. The application of wear-resistant and tribologically adapted thin-film sensors enables measurements in areas which were previously difficult to access.
Our thin-film-based sensor technology offers ideal prerequisites for application-oriented solutions in all aspects of industrial production processes. In recent years, there has been an increasing demand from industry for sensor technology which is used directly on component surfaces in contact with the workpiece in order to be able to record local measurement data, also during the process. Thus, the focus of our current developments lies on individually adapted sensor technology for comprehensive digitalization of autonomous and self-controlling production systems.
At the Fraunhofer IST, we develop multifunctional thin-film sensor systems for the local measurement of pressure and temperature distribution on surfaces, for example of tools. This involves a wear-resistant multilayer system which can record the measurement data – particularly in highly stressed areas and on complexly shaped surfaces. In collaboration with our customers, we create an individual sensor design in order for the modules to be easily integrated into existing machines and for the layer system to be applied directly to surfaces of 2D and complexly shaped 3D components. On the basis of differing physical operating principles, we introduce thin-film-based sensors and sensor systems into the most diverse applications, focusing thereby on highly stressed areas and harsh environmental conditions. For the production of our sensor technology, we cover the entire process chain from substrate pre-treatment, through cleaning and coating, and on to the final calibration. At the Fraunhofer IST we have acquired extensive expertise in the generation of microstructures; for this, we apply a wide range of structuring processes and techniques in our dedicated clean room.
The thin-film systems developed at the Fraunhofer IST enable you to acquire in-situ real-time process data in main load zones for the optimization of simulation and production processes as well as for condition monitoring. If you are interested, please do not hesitate to contact us.
Anna Schott M.Sc. / Group Manager
In the future, our sensor technology will be further developed for new fields of application in the area of energy technology and electromobility. In parallel, the necessary steps will be taken to scale up current solution approaches for successful technology transfer to industry in line with Fraunhofer's self-conception as an industry-oriented research partner. In order to achieve this, processes capable of handling large numbers of units and the associated production technologies will be developed and set up as flexible manufacturing. The focus hereby is on the digitalization of the entire process chain through to the development of cyber-physical systems. Through tribological optimization of the entire process chain, the achieved efficiency gains can provide a direct contribution towards the achievement of sustainability goals.