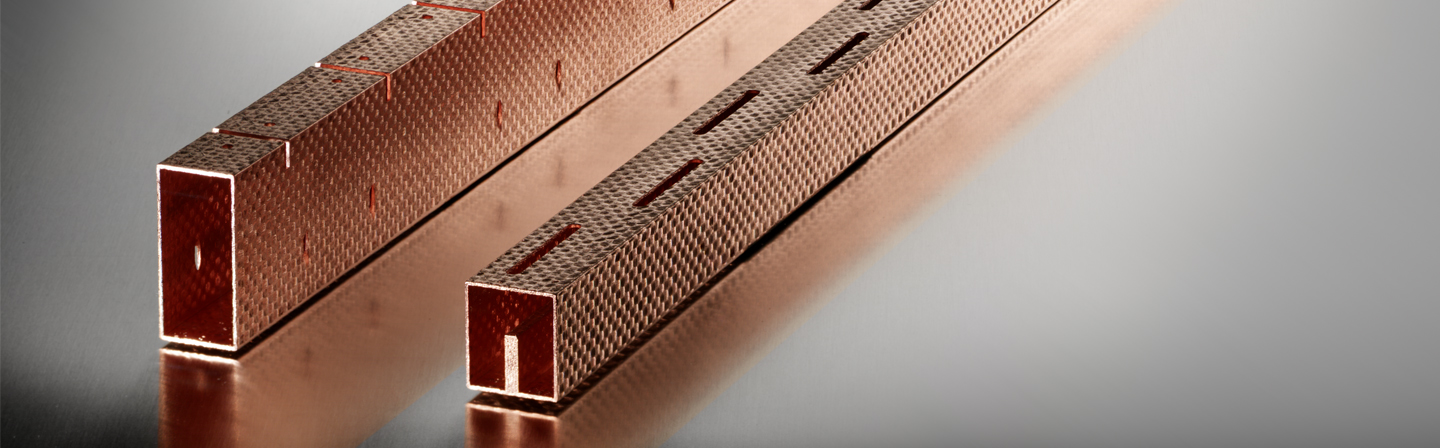
Active exploration of space serves not only the study of fundamental laws of physics but also real applications such as the investigation of living conditions on distant planets. Almost all of today's missions rely on optical instruments. Hyperspectral cameras of the Sentinel satellites can record the state of the earth's atmosphere or the earth's surface very precisely from orbit. With the construction of the ESA “Moon Village”, plans are being made to send people to the Moon for a longer period of time in order to conduct research there.
The Fraunhofer IST develops and implements surface technology solutions. (Electro)-chemical processes are used in order to extract usable metals as well as life-enabling oxygen from lunar regolith. Novel concepts based on conductive thin film systems allow automated removal of dust from surfaces. We are developing processes to produce energy storage systems as well as propellants from lunar material. Space-specified optical precision coatings are realized with the latest coating processes at high TRL. Components made of lightweight materials such as CFRP can be electroplated.
With scientific expertise and systems engineering, knowledge of the space-exploration market, and contacts to agencies such as DLR and ESA as well as to the relevant companies, the Fraunhofer IST can help you in the realization of your projects and ideas.