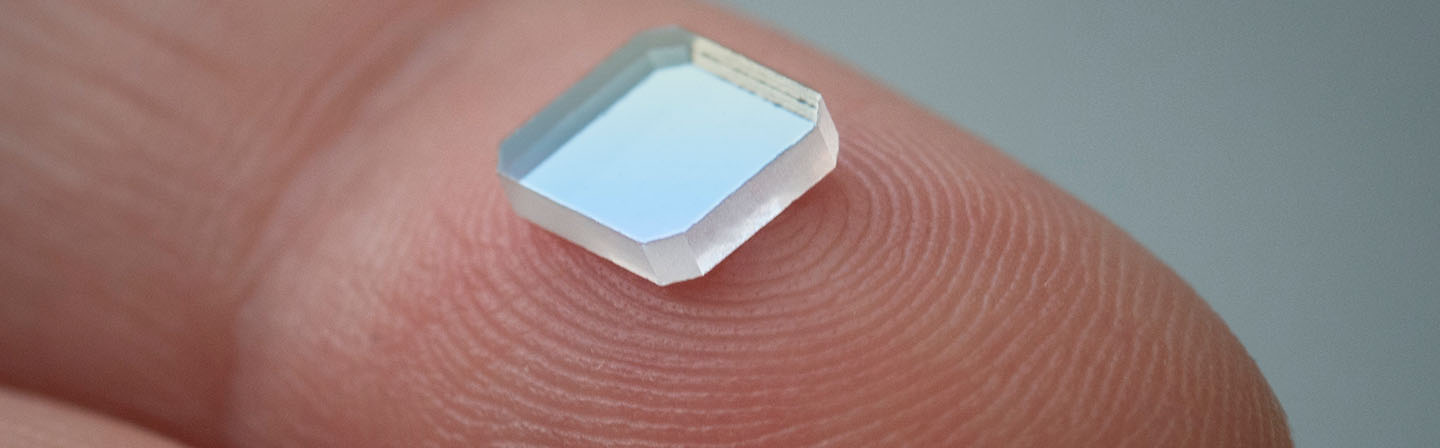
The Fraunhofer IST received the order for the coating of bandpass filters for the Mars2020 mission back in 2016. The coating materials had to be characterized in advance with regard to radiation stability and the filter had to withstand many cycles in the thermal vacuum test. They were coated onto glass which was to be bonded to the sensor.
A design was calculated for a bandpass filter with a central wavelength of 950 nm, which also only exhibits a small shift at an angle of 15°. For this purpose, tantalum pentoxide and silicon oxide were selected on the basis of the influence of radiation. The layer stack comprised 137 layers with a total thickness of 14 µm. The deposition was carried out on the production system EOSS® with control and layer thickness control by the software MOCCA+®. Subsequently, the quartz glass pieces had to be cut to 5.1 x 6.3 mm in order to achieve a rimless coating.
The filters passed all pre-tests and were integrated into the RDS system. Here, they had to pass another 3000 thermal cycles from -135 to +45 °C over several years to simulate the mission time on Mars. They contributed towards the dust analysis carried out after the Perseverance Rover landed in February 2021.
»The sensor is operating really well. All elements of RDS passed a very intensive test we carried-out during 4 years to ensure their survival to more than 3000 thermal cycles from -135 to +45 Celsius deg. That was probably the most demanding qualification test.«
Ignacio Arruego Rodriguez, Project Manager at INTA, 22.02.2021, after the Rover had landed.
»Those filters you made are in our Radiation and Dust Sensor, which is safely on Mars since last Thursday. You can (and should) be proud of this fact, to which you have contributed.«
Jose Antonio Rodriguez Manfredi, INTA's MEDA System Project Manager, 24.02.2021.