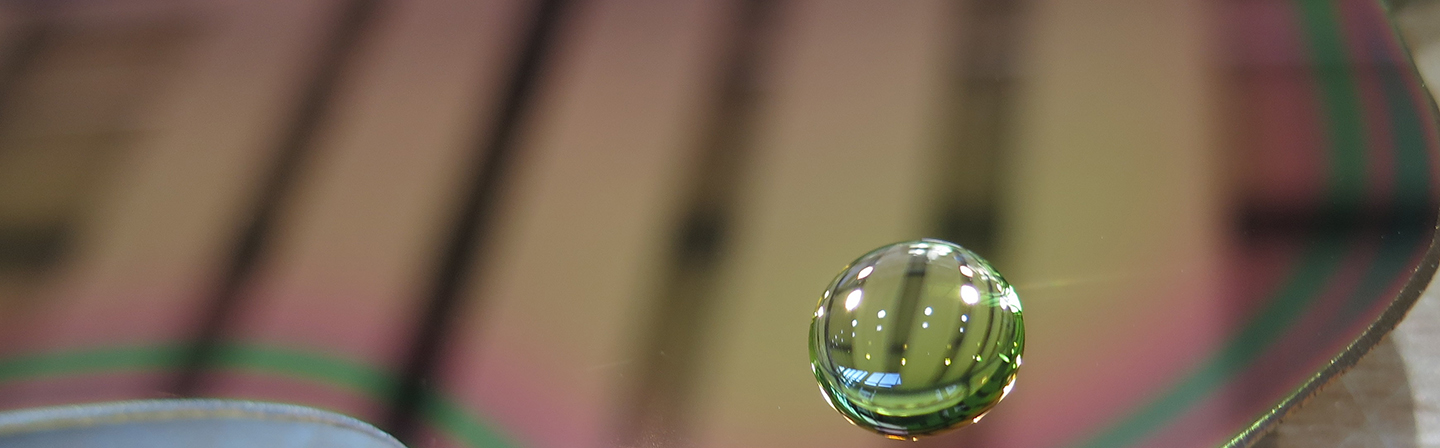
The reliable production of high-quality and optical plastic products with very smooth surfaces is often massively impeded or even prevented by the adhesion of polymers to the polished mold surface. Within the framework of the IGF project “GLANZFORM”, the Fraunhofer Institute for Surface Engineering and Thin Films IST was successful in further developing anti-adhesive coating systems for tools. These enable a significant reduction in demolding forces without impairment of the quality of the component surface.
In injection molding or hot-stamping processes for the production of high-quality plastic products, new innovations are constantly required as a result of rising customer demands together with ecological and economic parameters such as increased requirements for sustainability and efficiency. Products such as optical, medical and microsystem-technology components, as well as credit and ID cards and decorative and interior elements with high-quality or optical surfaces are subject to the demand for the highest surface quality. This, in turn, is primarily determined by the surface of the molding tool and its reliable molding process. With increasing surface quality of the mold, however, the molding forces increase disproportionately, which can severely impair component quality and prevent efficient production.
One means of reducing molding forces during plastic molding is to coat the tool with an anti-adhesive layer with the lowest possible surface energy and low polar content, such as silicone-containing coatings, or the use of release agents, which are utilized in many production processes.
For many plastic-molding processes, however, satisfactory and flexibly applicable adhesion-reducing coating solutions which fulfill the high demands on surface quality have not existed up to now. Many established coatings lead to a roughening of the polished mold surface and are not sufficiently adhesion-reducing or wear-resistant.
The task of the Fraunhofer IST within the described project was the development of tool coatings which reduce adhesion or molding forces. This was achieved through chemical means by minimizing the intermolecular interaction between the tool surface and the polymer and simultaneously through mechanical means by setting a defined roughness in the sub-micrometer range. For this purpose, PVD/PECVD (physical vapor deposition/plasma enhanced chemical vapor deposition) combination coating systems consisting of Cr/CrN and a-C:H:Si:O layers (SICON®) were developed. It was possible to adjust the topography of the Cr/CrN layers by means of parameter variation during PVD magnetron sputtering in such a way that they could serve as a target-oriented template layer for the anti-adhesive SICON® layer.
Through the developed PVD/PECVD combination coating systems, the associated modification of the surface chemistry and supplementary reduction of the adhesion forces via controlling of the contact surface by means of targeted adjustment of the roughness, it was possible to achieve an adhesion-force reduction of approx. 60 percent compared to highly polished steel surfaces in the hot-stamping of polyethylene terephthalate (PET). With this coating system, it was possible to demonstrate improved demolding in the hot-stamping of optical components without any significant deterioration in the surface quality of high-gloss surfaces in an industrial environment.
This was also achieved for the first time in the specific area of very smooth surfaces (Sa ≤ 20 nm), which are typical for high-gloss plastic surfaces. As a result, new and innovative approaches to the design of tool surfaces are possible in the application, which could make the use of release agents or molding-compound additives for easier demolding superfluous in the future. These advantages can also be exploited by coating companies, whose production results can be optimized not only by adjusting the surface chemistry but also through the adjustment of the surface topography as a further correcting variable.
The developed approach, consisting of topography adjustment and adapted coating, is to be further developed for other coating systems, in particular for tools in polymer molding. In collaboration with the project partners, the Fraunhofer Institute for Structural Durability and System Reliability LBF in the area of polymer molding and the Fraunhofer Institute for Mechanics of Materials IWM in the area of modeling, an expandable and openly usable database for process, material and tool-surface designs for more efficient, demolding force-optimized and sustainable plastic-molding processes is to be developed.
The IGF project “Glanzform” (19545 N) of the Forschungs- vereinigung Forschungsgesellschaft Kunststoffe e. V. (FGK), Haardtring 100, 64295 Darmstadt, Germany was funded by the German Federal Ministry for Economic Affairs and Energy via the AiF within the framework of the program for the promotion of joint industrial research and development (IGF) on the basis of a resolution of the German Bundestag.
This article is part of the annual report 2020.