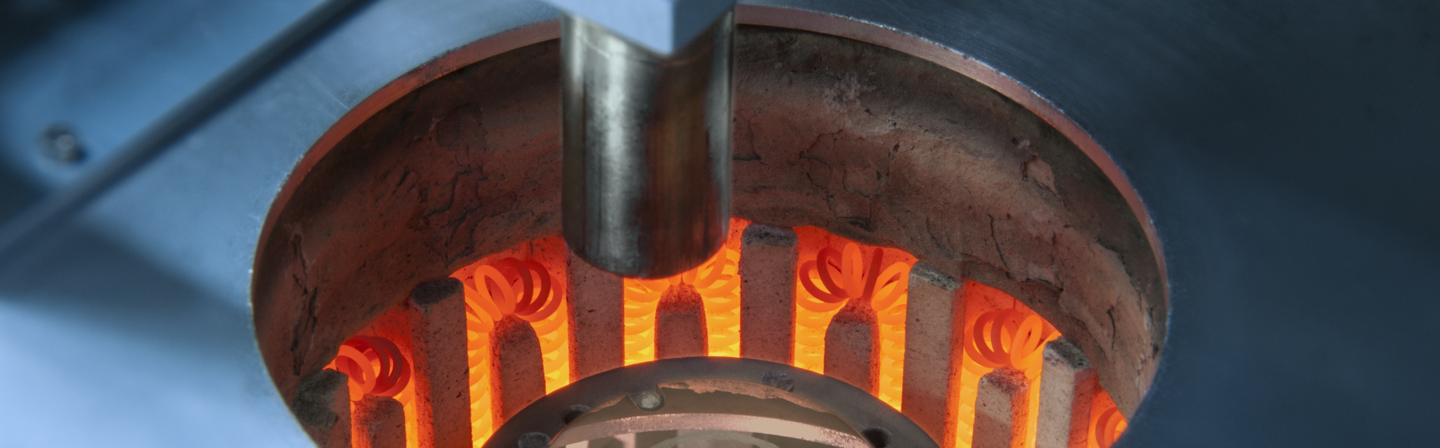
The utilization of high-temperature materials such as nickel, molybdenum or cobalt-chromium base alloys is indispensable for many applications. This applies, for example, to thermally highly stressed forming tools or components for engine and turbine construction. Whilst the materials usually fulfill the strength requirements, in many cases the friction and wear behavior is unsatisfactory. The Fraunhofer IST has therefore developed surface-layer treatments which significantly improve the friction and wear behavior of these materials.
One significant application of the aforementioned high-temperature materials is forming tools for the hot-forming of high-strength titanium alloys and titanium aluminides. At temperatures of up to 1200 °C, components for turbine and engine construction as well as medical technology are produced from them. At forming temperature, the tools must exhibit a higher strength than the materials to be formed at low friction, whilst simultaneously ensuring sufficient wear resistance in order to enable economical production.
One possibility for increasing the hardness and wear resistance of metallic materials concerns diffusion processes such as nitriding and boriding. In these processes, nitrogen or boron diffuses into the material and alters the material properties in the peripheral zone. Prerequisites for this are that either nitrogen or boron is provided on the surface in a suitable reactive form, that it can penetrate into the material, and that the temperature is high enough to enable diffusion. Depending on the material to be treated and the process parameters, compound layers and precipitates can be formed, which lead to hardening of the surface layer. With nitriding, the reactive nitrogen is provided predominantly from the gas phase, often with plasma support. With boriding, powdered or paste-like dispensing media have been used almost exclusively up until now. The residues have to be laboriously removed following the process. For steel materials, these nitriding and boriding processes are state-of-the-art. Occasionally, nickel base materials are also boron-treated with powdered or paste-like dispensing media.
In an internal Fraunhofer research project, the application of plasma nitriding processes and a gas boriding process, newly developed at the Fraunhofer IST, was investigated regarding the surface-layer treatment of nickel, molybdenum and cobalt-chrome base alloys. For each of the materials, suitable treatment parameters could be identified, in which well-adhering surface layers with high hardness are formed. Through subsequent heat treatment, their properties can, in many cases, be further improved. The adjacent Figure in the middle shows the forming surface layer using the example of a gas-borated molybdenum base material.
The sample hardness was determined using a micro hardness tester from Fischer. A very small test load is thereby applied to measure the hardness of thin layers with spatial resolution. For the evaluation of the friction and wear behavior of the surface-layer-treated high-temperature materials, a high-temperature tribometer is available at the Fraunhofer IST with which pin-on-disc tests can be carried out at temperatures of up to 1000 °C under a defined inert gas atmosphere or ambient air in differing load ranges. The coefficient of friction, the occurring wear, and any chemical and structural changes to the materials are evaluated.
For nickel, molybdenum and cobalt-chromium base alloys, considerable increases in hardness in the peripheral zone could be achieved through adapted plasma-nitriding or gas-boriding processes. In the case of gas-borated nickel and molybdenum base alloys, the hardness could be increased to between 2500 and 3500 HV. Simultaneously, the coefficient of friction at forming temperature was reduced by up to 80 percent compared to high-strength titanium alloys and titanium aluminides. Material build-up, one of the main causes of failure in untreated forming tools, could be completely avoided. Application tests in the hot-forming of titanium aluminides for the manufacture of turbine blades are currently in preparation.
This article is part of the annual report 2019.