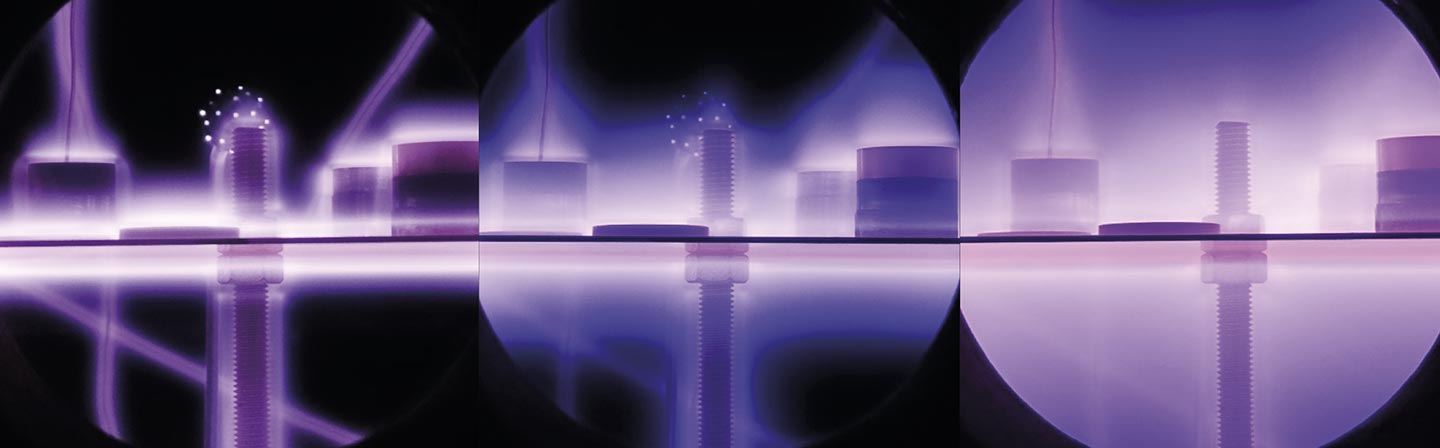
During the production of cutting tools, state of the surface and edge-layer arise which require the most efficient cleaning procedure possible in order to allow the subsequent coating. With the aim to avoid the use of suitably aggressive wet-chemical cleaning agents and simultaneously create further technological advantages, the Fraunhofer IST successfully participated in a DBU joint project, together with partners from industry and research, in which an alternative cleaning process chain was developed and evaluated.
The developed combinations of balanced pretreatment processes enable a high cleaning effect with significantly reduced environmental pollution. Simultaneously, additional technological functions, such as the adjustment of the cutting-edge geometry for geometrically complex cutting tools, are possible. This results in an economical alternative to conventional cleaning processes.
In order to increase the process reliability of the subsequent vacuum coating processes during production, the following individual process steps were examined in different combinations and evaluated by investigating the wear behavior of coated tools in machining tests:
As a further development of the state-of-the-art in production, a two-stage cleaning concept was selected for the aqueous cleaning process in such a way that the greatest possible effect can be achieved with the smallest possible application quantity. The intelligent combination of active ingredients is biodegradable and retains the pH values of the utilized aqueous cleaning agents within a moderate neutral range.
Working with the CO2 snow jet, which is accelerated to supersonic speed, enables the efficient and gentle removal of particulate and film contamination such as dust, residues of polishing pastes, oils or cutting emulsions. This process can be automated and locally focussed for the cleaning of geometric areas which are difficult to access.
With plasma-electrolytical polishing (PEP), the component to be treated is cleaned and polished in an electrolyte of non-toxic salts and water by applying a voltage of several 100 V. In addition to very good cleaning results, burrs and impurities are removed in the same process step. Furthermore, the cutting-edge radii of the tools can be specifically adjusted.
For the final step of the pretreatment, the substrate surface at nanometer scale is cleaned from any chemical compounds under vacuum conditions by means of plasma-chemical and plasma-physical processes and chemically activated. This plays an important role, in particular as regards the bonding or adhesion of subsequently applied layers. Decisive for effective cleaning are the prevailing plasma conditions, which can be modified in wide ranges by varying the pulse geometry, acceleration voltages and plasma power (see Figure above).
In the development of the process chain, various individual process combinations were applied to artificially contaminated cutting tools. In order to create the best-possible comparability, a synthetic reference contamination consisting of oils, fats, particles and suspensions used in the reference production chain was developed. Prior to the evaluation, the tools were qualified with regard to cutting-edge radii and surface roughness as well as coating adhesion. The maximum tool life of the tools was then determined in a machining test.
An evaluation of the results shows the direct influence of the individual processes in the respective chain:
This article is part of the annual report 2019.