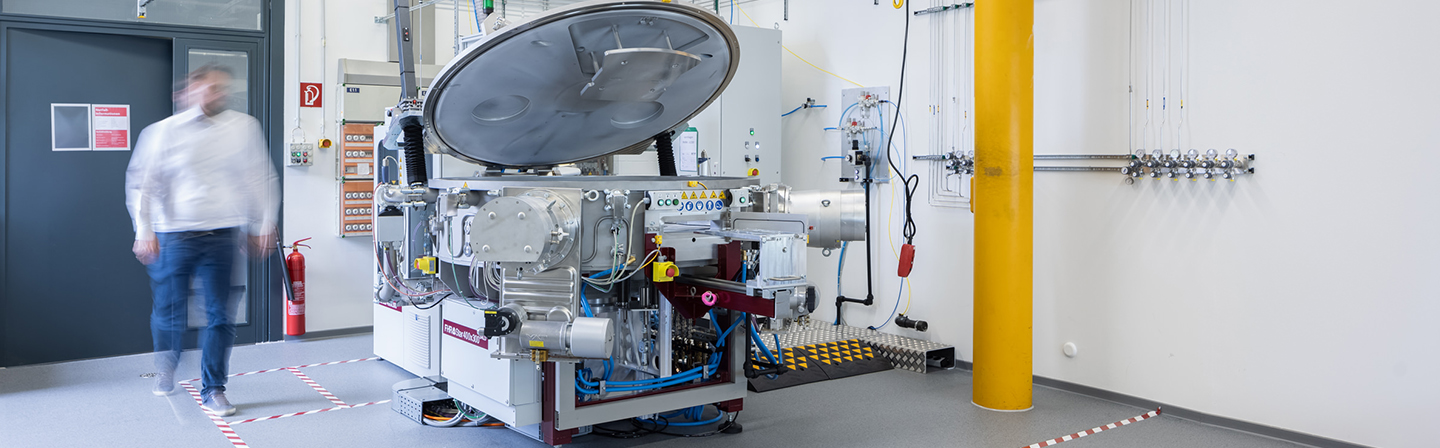
Robust and high-performance - these are two requirements which are repeatedly stipulated in plant and mechanical engineering as well as in toolmaking. Often, the only option for implementing these demanding goals is the utilization of surface treatments and coatings which are adapted to the materials being used and the conditions under which they are applied.
In order to comply with the increasing requirements in almost all areas of plant, machine and tool construction, the Fraunhofer IST focuses on material composites consisting of high-tech constituents and material-specific surface finishing. Surface technology can, however, do even more: It offers new approaches to the design of components, and permits the utilization of other materials or even the elimination of lubricants and release agents.
Starting from a detailed system analysis, we then develop adapted material and surface solutions for our customers. For this purpose, we employ a wide range of coating technologies and layer materials. Complex requirement profiles can also be fulfilled in this way. Even sensory functions can be implemented via coatings on tools and components in highly stressed zones and utilized for monitoring purposes.
We offer you system evaluation and industrial solutions from a single source!