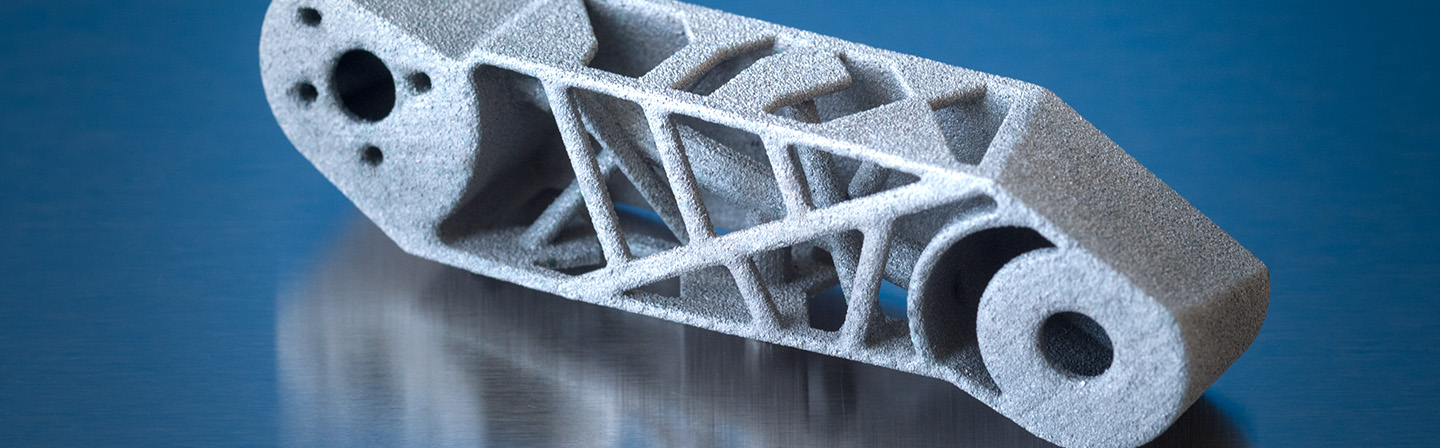
Additive manufacturing as a production process for the manufacture of parts and components is already playing an important role today - and this role will become even more significant in the future. The design of highly complex geometries paired with the most diverse materials, such as metals, ceramics and plastics, opens up a variety of possibilities which are not possible with traditional manufacturing processes such as turning or milling. One weak point of additive manufacturing is currently presented by the surface, which can vary greatly depending on the manufacturing process. This can lead to problems in the utilization of the components and may necessitate surface treatment. At the Fraunhofer IST, additively manufactured components are therefore galvanically metallized and furnished with the desired surface properties.
Until now, so-called structural components, i.e. brackets, connecting pieces, etc. have been manufactured from metal using conventional processes such as turning or milling. These parts are heavy and, as a result of the manufacturing processes, not always optimal as regards design. If these components are manufactured by means of additive processes, they can be designed more advantageously, for example to save weight or to achieve improved mechanical properties. If the metal material is replaced by plastics, the weight can be reduced even further. Plastics, however, do have a number of disadvantages compared to metals; they are, for example, not conductive without an appropriate coating.
In the research project AMPFORS (Additive Manufacturing of Polymer Parts for Space), funded by DLR within the framework of the “InnoSpace Masters” program, the Fraunhofer IST, in collaboration with OHB AG in Bremen and Rauch CNC Manufaktur in Baden-Baden, is therefore investigating how the metallization of additively manufactured plastic components can improve their properties. These components are to be used in space travel and must therefore fulfill a multitude of special properties. As an example, polymers in a vacuum tend to outgas water or unreacted monomer, which can deposit on optical instruments and impair their function. The surfaces must also be conductive in order to prevent electrical charging of the parts in space.
Within the project, components were manufactured from the high-performance plastic polyether ether ketone (PEEK) and the construction plastic polyamide (PA) with the aid of the additive manufacturing process SLS (Selective Laser Sintering). These parts were subsequently galvanically metallized and tested at the Fraunhofer IST. A nickel coating with differing layer thicknesses of 0 - 150 µm was applied as the metal. Initial investigations have shown that the metal coatings can be firmly applied to the plastic surfaces. The adhesion test ECSS-Q-ST-70-17C, a thermal-shock test important for space applications, was successfully executed. It could also be shown that the mechanical properties are dramatically improved through metallization. The modulus of elasticity for uncoated PEEK, for example, increases from 4.8 GPa to 20 GPa with a coating thickness of 150 µm nickel on the plastic. The situation is similar with polyamide, where the modulus of elasticity increases from 1.5 GPa to 12.5 GPa (see opposite figure). The flexural and compression moduli increase accordingly.
Within the further scope of the project, the extent to which the possible geometry optimization impairs the metallization must be clarified. Galvanic processes suffer from the fact that complex geometric structures can only be metallized to a limited extent as a result of the necessary electric field often being shielded. Chemical metallization processes can be the solution.
This article is part of the annual report 2019.