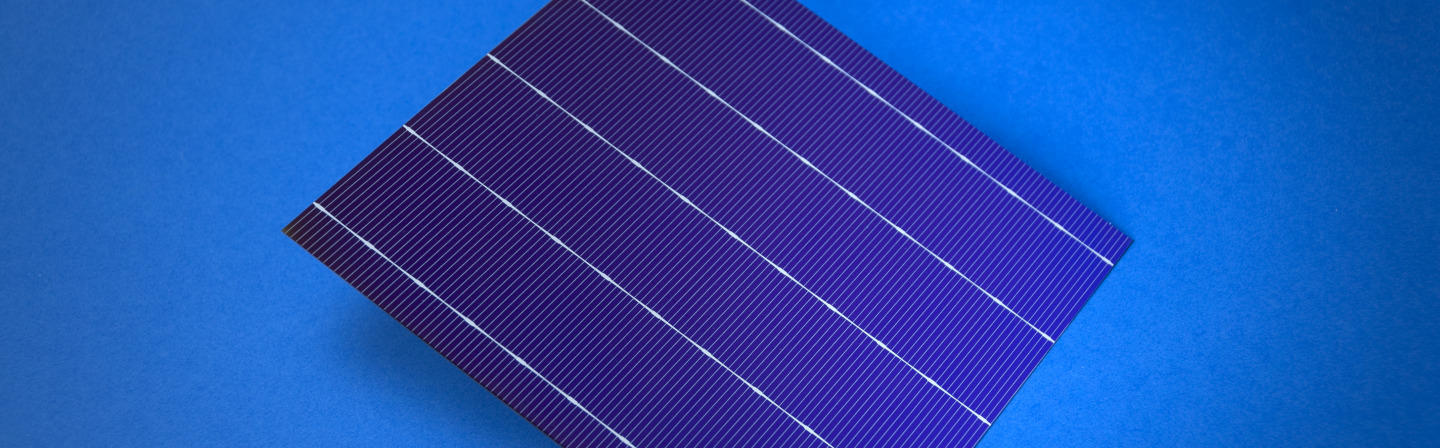
Vehicle-integrated high-performance solar cells can only be used successfully if they meet the demanding requirements of automotive engineering. This is why high efficiency at low cost, visual appearance (color, impression) and the challenges of roof glazing in vehicles (e.g. hailstorm test, resistance to temperature and climatic changes) are of prime importance.
During the project, highly efficient heterostructure solar cells were manufactured in which all the necessary silicon films were produced by the Fraunhofer IST using hot-wire CVD. Compared to the PECVD processes used previously, HWCVD represents a more cost-effective alternative for the production of functional films due to the simpler system concept, its high deposition rates (up to 7 nm/s) and the greatly improved gas utilization (> 80 %).
The successful fabrication of SHJ solar cells by means of HCVD was demonstrated on large M2 wafer areas (156 x 156 mm²). Despite several interruptions in the process chain (wafer etching and cleaning, TCO deposition, metallization carried out by partners), cell efficiencies of 19.75 % were demonstrated on this wafer size.