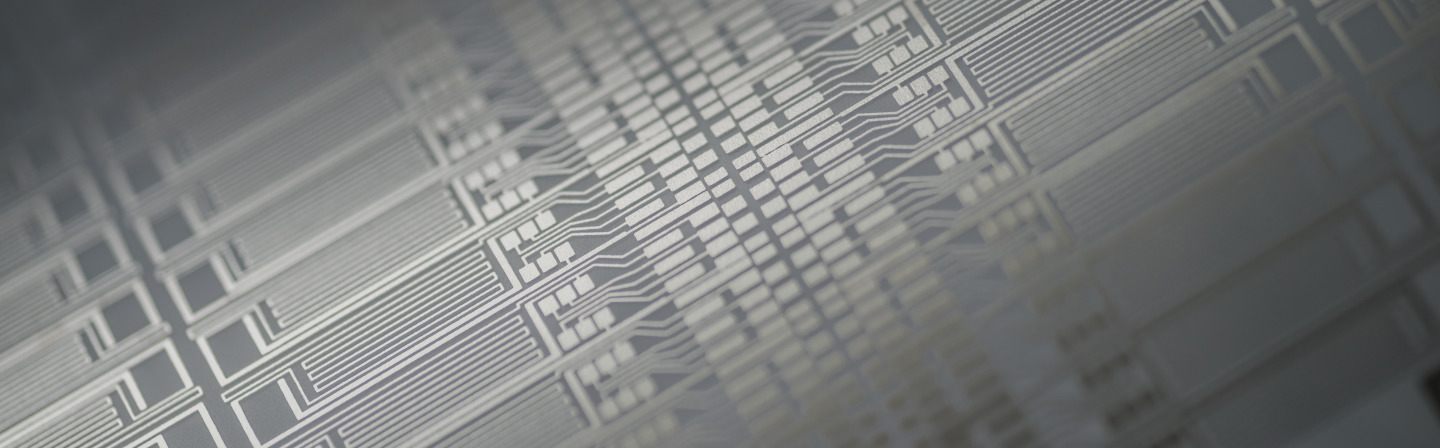
Local functionalization plays an important role in many applications. These range from the production of surfaces for the biomedical sector (biochips, DNA chips, protein chips, diagnostic chips) through to the subsequent metallization, such as the production of circuit carriers, RFID antennas or biosensors.
At atmospheric pressure, plasmas can be generated in very small volumes with dimensions of just a few micrometers, enabling surfaces to be functionalized locally. One innovative process for the local modification of surfaces is plasma printing: Through a structured dielectric, cavities are formed in which the plasma develops. The typical dimensions of the cavities range from several 10 μm up to several 100 μm. In addition to the site-selective modification of surfaces, the process allows structured layer deposition or functionalization.
Depending on the selected discharge conditions, a variety of functional groups can be imprinted on the substrate like a stamp. Suitable substrates include polymers, glass or silicon. The plasma printing process can be used to produce surfaces with arbitrary geometries, for example arrays of spots, with special surface properties such as hydrophilicity, hydrophobicity or with targeted chemical functionalization.