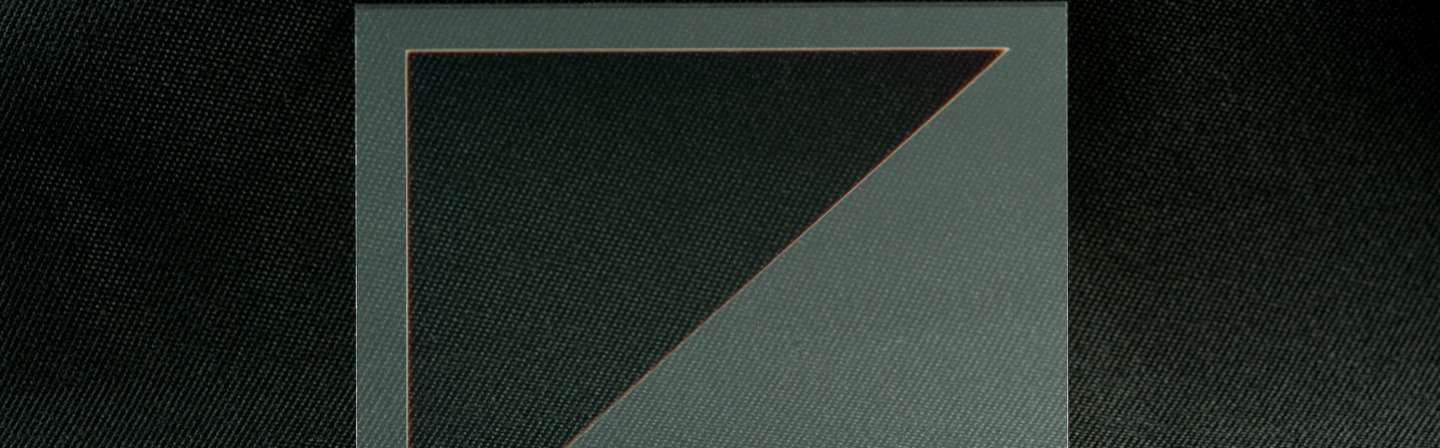
At the time of the project launch, it was not clear as to whether silicon oxide layers SiO2 could be deposited over a large area using the hot-wire CVD method. The reaction of the wires with oxygen posed a potential risk, as it leads to oxidation of the wires and has a negative influence on the stability of the process. The goal was to produce a low-stress, optically high-quality SiO2 layer.
In the hot-wire CVD process, electrically heated tungsten wires in the range of 1900 °C - 2100 °C were utilized within a vacuum vessel to dissociate SiH4 and produce the metal oxide under the addition of oxygen. For the development of the silicon oxide layers, a statistical design of experiment (DOE) was employed in order to perform a parameter study on quartz glass. Gas compositions, pressures and temperatures were thereby taken into account. For the substrate, plastics can also be used.
The highly transparent layers could be produced with low compressive stresses The following layer properties were achieved: high transparency for d (SiO2 = 380 nm) T250 nm > 89 % on quartz, low compressive stress for d (SiO2 = 2.5 μm) σ < 170 MPa (low residual stress), low roughness for d (SiO2 = 2.5 μm) < 6 nm, deposition rates > 2 nm / s, tungsten concentration cW ≤ 0.2 atom%.