Wear protection of highly stressed tool surfaces in extruders
For the economical and ecologically sustainable processing of plastics, long-lasting and correspond-ingly wear-resistant machine components are required. The Fraunhofer Institute for Surface Engi-neering and Thin Films IST and the Southern-German Plastics Center SKZ are working together on the AiF project “Surface modification for the reduction of wear on highly stressed tool surfaces in extruders for plastics processing (extruder wear)”.
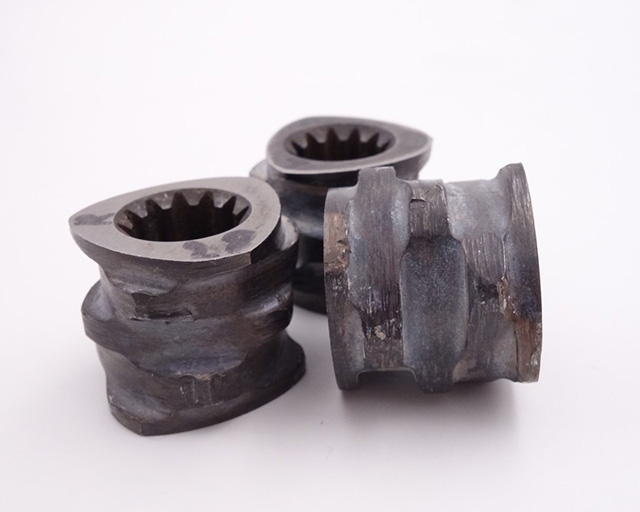
The research project started in December 2021. Surface modifications on the basis of PACVD coatings and boron diffusion treatments are being investigated. The project addresses the requirements of the companies involved in the value chain and, in particular, SMEs, such as compounders and surface finishers as well as equipment manufacturers.
Requirements for the coating process
The aim is to select a coating process that can ensure an optimum mixing effect with maximum throughput and minimum energy input. A number of requirements must, however, be thereby fulfilled. Firstly, the surfaces of worm shafts and extruder nozzles are subject to very high stresses caused by modern plastics, whose functional properties are increasingly being enhanced with the aid of fiber reinforcements, fillers and additives. In addition, corrosive ambient conditions can intensify the stress on the components. Secondly, there exist high demands on productivity in terms of the pressures that can be realized and the short throughput times that are required. Owing to the difficult geometric accessibility, the complex geometry of nozzles and screw elements limits the selection of suitable coating processes for wear-protection systems.
As a suitable process, plasma-activated chemical vapor deposition (PA-CVD) is initially being investigated, which enables thin hard coatings by means of plasma-chemical conversion of gas mixtures. In special processes, multilayer coatings containing titanium diboride and titanium nitride phases can be produced. These exhibit a nanocomposite structure which is favorable for mechanical stress. The hard and chemically very stable titanium diboride present in the phase mixture counteracts adhesive and corrosive attack.
The second process being considered allows boron to diffuse into the edge zone of the tool by means of a thermochemical edge-layer treatment. This results in the formation of hard and corrosion-resistant boride precipitates, which also offer great potential as regards fulfilling all the requirements of the application.
The approach - Step by step towards the goal
In the project, the wear mechanisms between the melt and the tool surface will initially be identified and evaluated. Subsequently, the different boron-containing surface modifications will be characterized and described on a laboratory scale in order to reduce wear on the surface. Finally, an evaluation under industrial conditions will be performed in order to verify the applicability.
Interested companies are cordially invited to participate free of charge in the project committee of the research project and to obtain information regarding the current results. The project is funded by the German Federal Ministry for Economic Affairs and Energy within the framework of the program for the promotion of joint industrial research (IGF) of the Forschungsvereinigung Kunststoff-Zentrum (Research Association Plastics Center) via the AiF on the basis of a resolution of the German Bundestag.
Last modified: