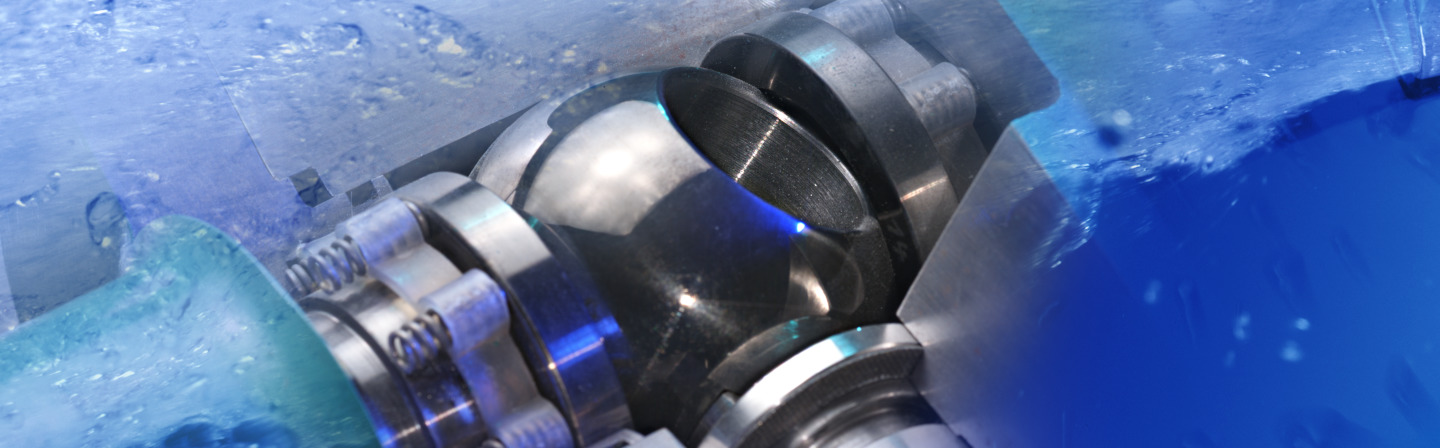
The chemical industry places the highest demands on surfaces and materials for components in its manufacturing processes, as material failures can lead not only to production stoppages but also to enormous damage to the environment - and can even endanger human life.
Using industrial plant-engineering technology, the Fraunhofer IST develops application-specific solutions for the production systems of the chemical and pharmaceutical industries. By combining different coatings and technologies, we are able to specifically fulfill the respective requirements in diverse applications. Low-wear and corrosion-resistant surfaces are particularly in demand here. Additional functionalization with, for example, non-stick coatings against contamination or biofouling can also be realized. Furthermore, we can apply thin, highly resistant thin-film sensor systems for the detection of temperature, mechanical stress or wear in order to monitor sensitive components and enable predictive maintenance.
We provide you with support in the development of new solutions!