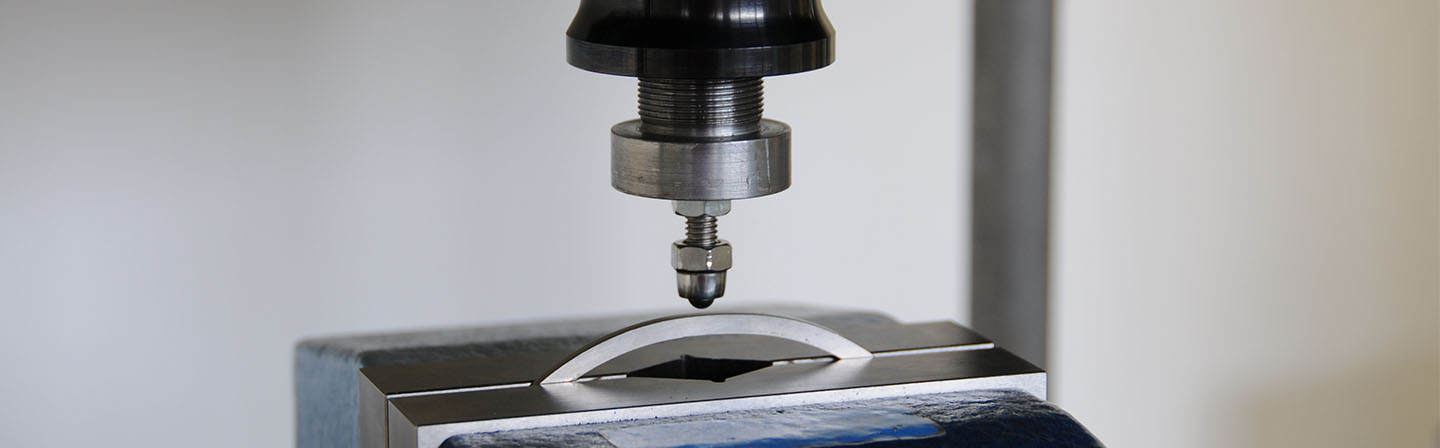
The impact test is a test method used to test the behavior of thick or thin layers, but also of solid materials with regard to permanent load. A fixed test ball exerts a long-term cyclic load (up to 1 million cycles) on the component to be tested. Depending on the area of application, the impact test can generate a fluctuating or repeated load (contact mode or lifting mode). The impact test provides a statement concerning the fatigue strength of the surface.
Die charakteristischen Prüfparameter beim Impact-Test sind:
The evaluation is usually carried out under an optical microscope or a scanning electron microscope, whereby deformations, cracking or spalling can be documented and quantified, including in cross-section if necessary.
Load series (e.g. 1, 2, 3, 4, 5 kN) or cycle series (z.B. 102, 103, 104, 105, 106 Zyklen) are possible in order to determine the damage threshold or service life of the materials.