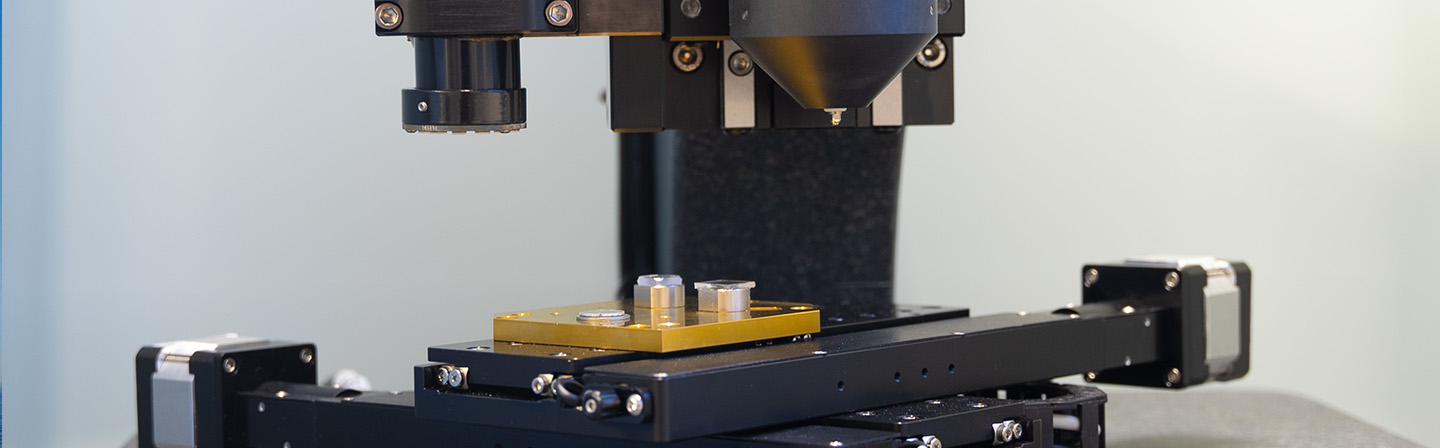
In recent decades, the demands placed on materials and their properties have increased enormously: Even for ultrathin coatings, it must be possible to unambiguously determine the hardness and the modulus of elasticity, for example. One common method of hardness testing is nanoindentation, which is also applied at the Fraunhofer IST. The existing range of possibilities at the institute has recently been significantly extended by a new nanoindenter.
A nanoindenter is deployed in order to determine the hardness, the modulus of elasticity and, if necessary, the viscoelastic properties of materials and thin films. This is performed by pressing a three-sided diamond tip into the surface in a controlled manner whilst continuously recording – with the highest precision – the necessary force and the penetration depth. From the measurement curves, the hardness and the modulus of elasticity of the material can then be determined - in some cases in dependence on the depth.
By means of the AFM mode, the surfaces can be imaged topographically both prior to and following indentation with the aid of the diamond tip, thereby enabling, for example, the exact position of an indentation to be verified retrospectively.
One special feature is calibration to the hardness of a reference material, which – in contrast to the common calibration to the modulus of elasticity – has the following advantages:
Furthermore, nano-scratch tests and wear tests can also be carried out with the aid of the scratch module.
Compared to the existing capabilities for hardness determination at the Fraunhofer IST, the new indenter device offers a number of advantages:
Hardness and modulus of elasticity are important parameters for all types of surfaces which are exposed to mechanical stress. These can be, for example, tribological protective coatings on milling cutters, tools, automotive components or machine elements, as well as paints, electroplating coatings, decorative coatings (scratch resistance) and nitrided or borated surfaces, display glass, etc.