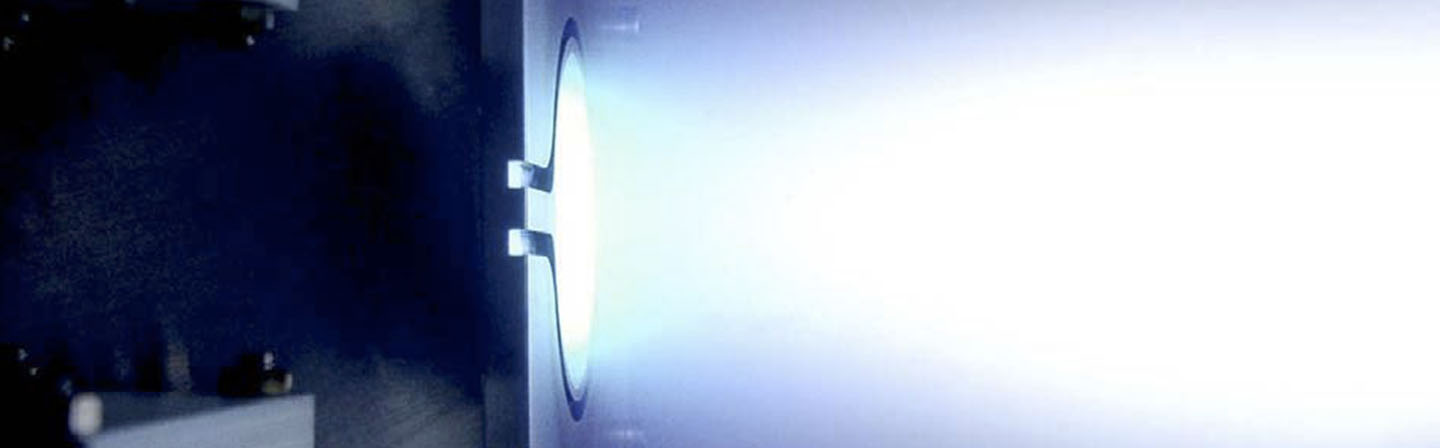
The Fraunhofer IST has been researching hollow-cathode glow discharge since the 1990s. In addition to a profound fundamental understanding of hollow-cathode processes, broad expertise has been acquired in the deposition of a wide range of functional coating systems using hollow-cathode technology. For process development and industrial application, the IST has developed hollow-cathode PVD and CVD coating sources. Our expertise in materials, sources, and equipment technology is utilized for customer-specific development and sampling.
Particular advantages of hollow-cathode technology lie in the economical deposition of porous coatings (e.g. thermal barrier coatings), magnetic materials, or generally functional coatings in a thickness range of several tens of micrometers. Furthermore, the deposition of valuable materials with almost 100 percent material transfer to the components is possible in special cases.
The Fraunhofer IST develops sources for gas-flow sputtering, a special form of hollow-cathode deposition. These are now used in the most varied applications all the way up to small-series production.
For the process development, hollow-cathode inline coating facilities were developed and constructed at the Fraunhofer IST. These facilities are used for research contracts and pilot production. In addition to source technology, the IST has acquired expertise in plant engineering which, together with plant manufacturers, is available for customer-specific solutions.