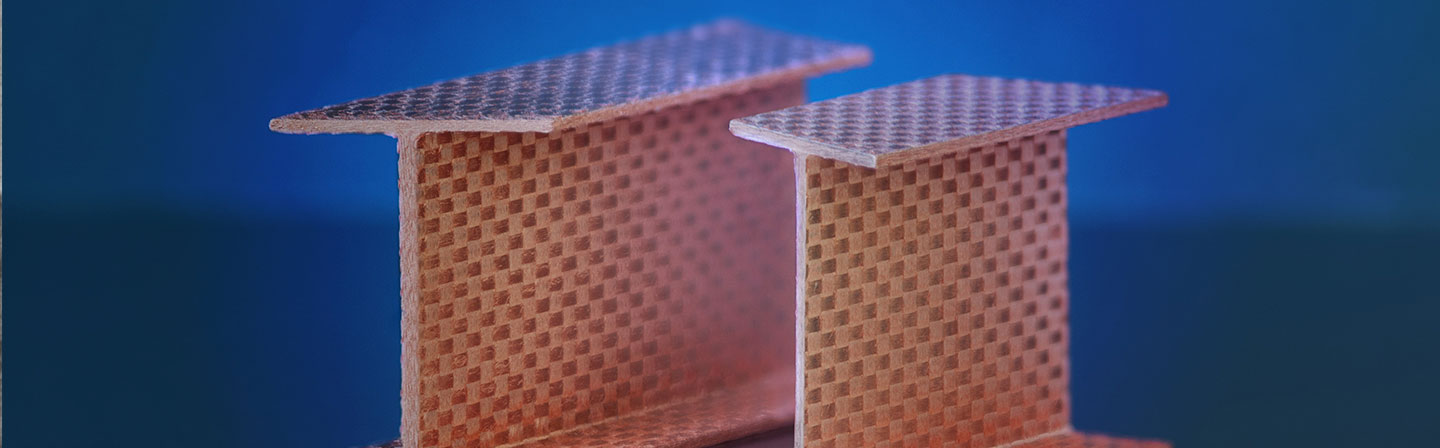
Galvanic plastic metallization is often still carried out via pretreatment with Cr(VI)-containing pickling agents. These pickling agents are considered toxic and carcinogenic and must be substituted following a transitional period in accordance with the European REACH regulation. The aim of the project was to develop a laser-based method in order to make the metallization process less harmful to the environment.
For the successful implementation of the project, it was imperative to obtain precise knowledge of the surface morphology of the conventionally pickled plastic, which was intensively investigated by means of scanning electron microscopy. The laser ablation process was modified in such a way that the plastic surface was a direct copy of the pickled surface. Extremely short laser pulses vaporized minute amounts of plastic on the surface, creating small craters that provided mechanical adhesion of the metal layer to the plastic in a similar way to chemical pretreatment.
The project has shown that with laser pretreatment, a new, low-environmental-impact method for metallizing virtually any plastic has been developed - without the need for chemical pretreatment. At present, however, laser processes are too cost-intensive for general use. The treatment of workpieces with complex geometries is also difficult.