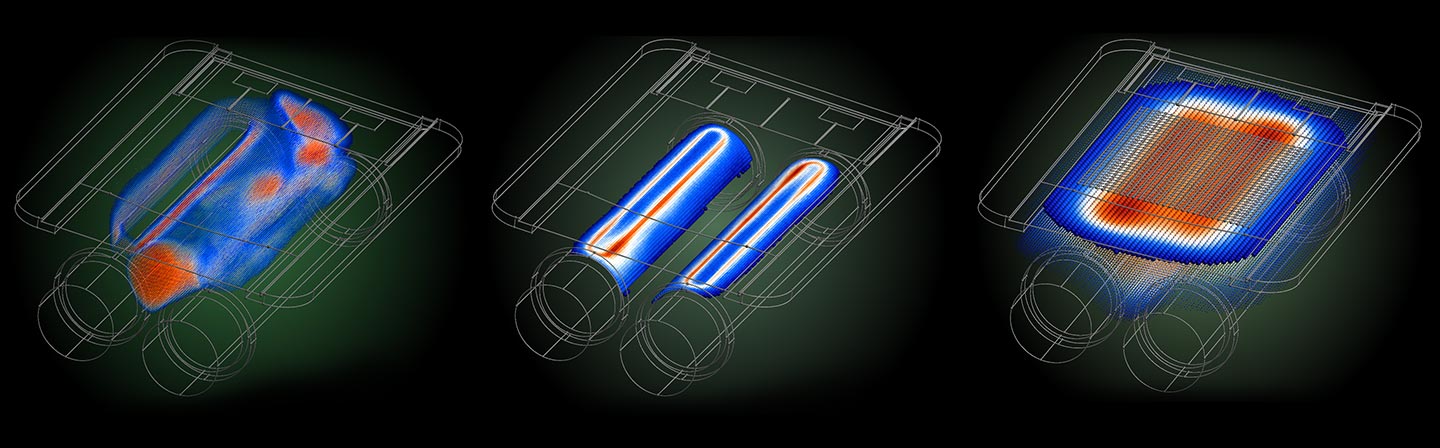
For the design of optical systems, it is advantageous to apply the required optical filter systems directly onto the curved surfaces of e.g. lenses instead of using separate flat substrates. This allows for the reduction of the quantity of components and, as a result, of internal reflections within the system. The system can be made lighter and more compact. However, the variable angle of incidence on curved surfaces leads to unintended color inaccuracies. In order to compensate for this, the optical filters can be applied with a specific layer-thickness profile. In the case of a convex lens, for example, this means that the layer thickness must increase from the center towards the edge. In contrast, in PVD processes such as magnetron sputtering, a reversed layer-thickness profile usually occurs on convex surfaces. We offer solutions for the application of desired layer-thickness profiles on curved components. A digital twin, based on data from a previous multi-scale process simulation performed at the Fraunhofer IST, enables the iterative optimization of shaper masks in order to solve this coating problem.
The coating process was realized on the EOSS® sputtering facility at the Fraunhofer IST. This system consists of two sputter compartments with dual cylindrical cathodes which are sputtered in argon, above which a fast-rotating turn table is mounted to which the substrates are attached. In an additional RF plasma source, the complete oxidation of the sub-layers takes place in an oxygen plasma. For rotationally symmetric 3D substrates, a special sample holder with built-in sub-rotation is utilized, whereby the layer-thickness profile is adjusted through special shaper masks at the compartment edges.
The multi-scale simulation model is used to specify the design of the shaper masks. The plasma, as well as the gas flow and transport of the sputtered particles, can be simulated using a kinetic software developed at the Fraunhofer IST in which the “Direct Simulation Monte-Carlo” (DSMC) and “Particle-in-Cell Monte-Carlo” (PIC-MC) methods are combined. Two practical problems thereby are the computational effort - approx. 1 day for DSMC and several days for PIC-MC - and the fact that the layer-thickness profile on moving substrates results from the addition of many sub-profiles from different positions. With the previous methods, this procedure is therefore considerably too time-consuming.
With a multi-scale approach, these problems are solved as follows: Firstly, the plasma and the sputter erosion profile at the target are determined using the PIC-MC method (see Figs. 1, 2). This information is subsequently used to simulate the transport and scattering of sputtered particles (see Fig. 3). The angle-resolved particle flow is thereby recorded in a plane a few millimeters below the substrates with a spatial resolution of 10x10 mm². Using this plane as a “virtual particle source”, the remaining particle transport up to the substrate is subsequently calculated using a simple ray-tracing approach, during which the shaper mask can simultaneously be taken into account in parameterized form. This approach is possible as the remaining distance lies below the mean free path and the scattering with the gas can therefore be neglected. The ray-tracing algorithm enables the calculation of a complete motion trajectory within a few seconds on a single CPU and can therefore be regarded as a “digital twin” for the coating process on 3D substrates.
A bandpass filter was deposited on a plano-convex spherical lens with a diameter of 20 mm and a curvature radius of 25 mm. In order to compensate for the spectral shift, a layer-thickness increase of 3.5 % from the center to the edge is required. The shaper mask geometry obtained through iterative optimization has a characteristic spiky form whose center point coincides with the lens trajectory (see Fig. 4, above). To test the model, the layer-thickness profile was first measured on non-rotating flat substrates (Fig. 4, below). It could be hereby determined that the assumption of a homogeneous target-erosion profile is insufficient (graph#1); good correlation can only be achieved with the sputter profile from the plasma simulation (graph#2). The bandpass coating was realized with an appropriate shaper mask and a rotating substrate holder. As can be seen in Figure 5, the spectral shift of the filter across the lens surface could be largely eliminated with the aid of the numerically optimized shaper mask.
The digital twin of the coating process on the EOSS® sputtering facility has been successfully validated and is utilized for further process and substrate geometries. It is also possible to coat a larger number of lenses simultaneously in a single batch.
This article is part of the annual report 2019.