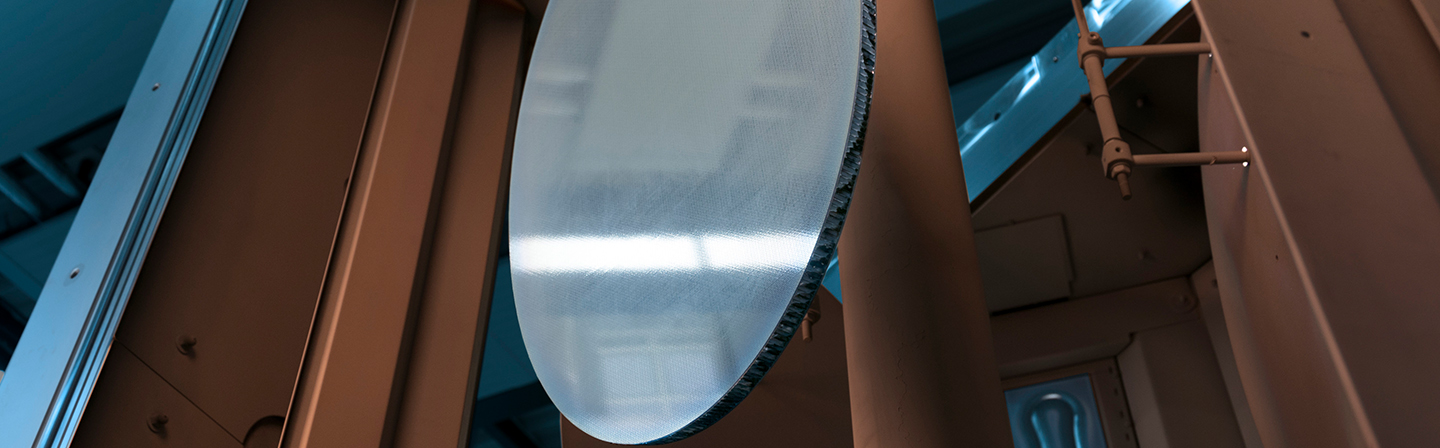
Mirror coatings play an important role in various fields such as laser or solar technology, telecommunications, astronomy, and medical or automotive engineering. The specific requirements for the coating vary depending on the application and can be related to aspects such as reflectivity, resistance to mechanical and chemical stress, special spectral requirements and temperature resistance. As a rule, either metal-based or dielectric mirrors are utilized. Metal-based mirrors are thereby characterized by high reflection capability in the entire visible spectrum, while dielectric mirrors can fulfill customized spectral requirements in that they can precisely reflect light in different wavelength ranges.
Based on your specific requirements and the substrate used, we develop suitable layer systems for your mirror coating and perform optical simulations. From our extensive portfolio of technologies (PVD, CVD, ALD), we select the appropriate deposition processes and optimize them in interplay with simulation processes, experiments and analytics. Our extensive expertise in the field of metallic depositions, their integration into layer systems, and their bonding to various substrates thereby comes into play. This is based, amongst other things, on the development of low-e and sun-control coatings. In our Optical Systems and Applications department, we use state-of-the-art system technology such as the EOSS® coating platform in combination with the MOCCA+® software for process control in the customized production of dielectric mirrors. In addition, we contribute our extensive expertise in surface technology, particularly in coating design and high-precision, automatically monitored and optimized deposition.
Our team is at your disposal to discuss your requirements with regard to mirror coatings or special issues, e.g. relating to the development and simulation of metal-based or dielectric mirrors. We are also happy to advise you on the optimization of existing coating processes.
We look forward to receiving your inquiry.