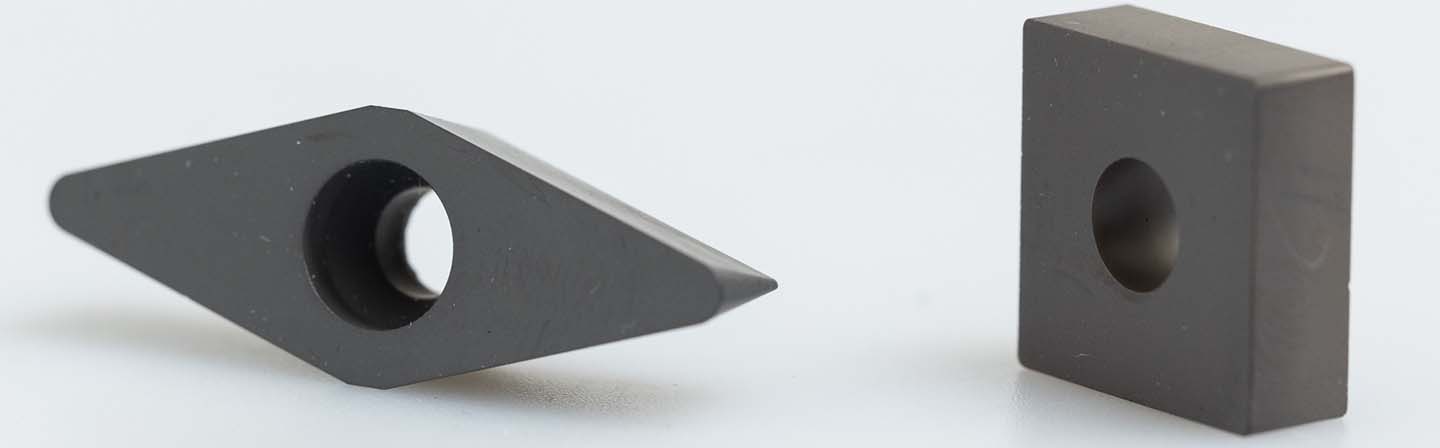
The texturing of tool surfaces and highly stressed components facilitates the targeted adjustment of tribological contact, going far beyond the possibilities of pure material and layer development. Tribologically effective structures and textures can have a decisive influence on the prevailing frictional forces. The machining of materials with a strong tendency to adhesion, for example, offers great potential. Within the framework of the Fraunhofer-internal project TexSpan, suitable methods for the production of laser-textured carbide indexable inserts coated with diamond or AlTiN were developed.
The economic and sustainable machining of aluminum and steel materials is of major relevance for automotive and mechanical engineering as well as for aerospace. The high adhesion tendency of many materials, however, poses a considerable challenge. Material adherence on the tool surface increases tool wear, reduces component quality and hampers productivity. Tribological structures for the reduction of material adherence have been identified in fundamental studies. For the technological verification and subsequent economic utilization, however, a systematic investigation of the influence of different texture geometries on the reduction of material adherence is still required. Furthermore, knowledge is lacking regarding an effective and economical manufacturing process for these textures. The conventional methods for shaping carbide tools, such as green machining or machining of sintered carbide via eroding or mechanical processes, are limited in the design freedom of possible structures and dimensions and are, in many cases, uneconomical.
In the TexSpan project, procedures for the texturing of chip surfaces by means of laser ablation were developed, and both the parameters for the processing of carbide tools and the processing of AlTiN and diamond coatings were researched. Subsequently, treatment sequences for the coating of laser-structured carbide were developed, including the investigation of micro-sandblasting as an optional pretreatment. The cleaning and chemical etching treatment, PVD deposition of AlTiN and hot-wire CVD deposition of diamond were also examined. As an additional optimization approach, run-in layers of amorphous carbon were tested. For the evaluation of the machining of stainless steel (V4A) and a hypereutectic aluminum-silicon alloy (AlSi17), structured tools were produced and subsequently coated. For this purpose, cell and groove structures were parameterized in a design of experiment (DoE) whereby the largest possible ranges of different structure sizes and machined-area fractions were investigated, which, from the point of view of the application, were judged to be of interest and practicable to implement.
Laser machining of carbide indexable inserts (WC-Co) with an ultrashort-pulse disk laser allows reliable, flexible and fast generation of cell, groove and other structures in the selected structure-size range from 25 µm to 100 µm with structure depths from 15 µm to 30 µm. With adapted pretreatment and coating processes, textured chip surfaces can be combined with both AlTiN and diamond of good quality and coating adhesion (see Figs. 1 and 2). The diamond-coated tools showed no visible wear when turning AlSi17. Whilst the experiments indicate a slightly reduced degree of material adherence on certain tools, no systematic correlation to the form of the various structures was apparent.
Diamond coatings with an additional run-in layer showed a significantly reduced tendency to form adherences in the turning tests with AlSi17. The best results were obtained in particular in combination with a high laser-machined area fraction (40 %) and large cell spacing (140 µm).
The treatment sequences developed for the production of structured and coated material surfaces can be transferred to other tool systems in machining and forming technology as well as to highly stressed components. The combination with adaptable multifunctional and run-in coatings enables adaptation to differing tribosystems, operating conditions and applications, which are to be developed in subsequent projects.
The TexSpan project, which is oriented towards small and medium-sized enterprises, was funded by the Fraunhofer-Gesellschaft. The Fraunhofer Institute for Production Systems and Design Technology IPK and the Fraunhofer Institute for Surface Engineering and Thin Films IST participated in the project.
This article is part of the Annual Report 2021.